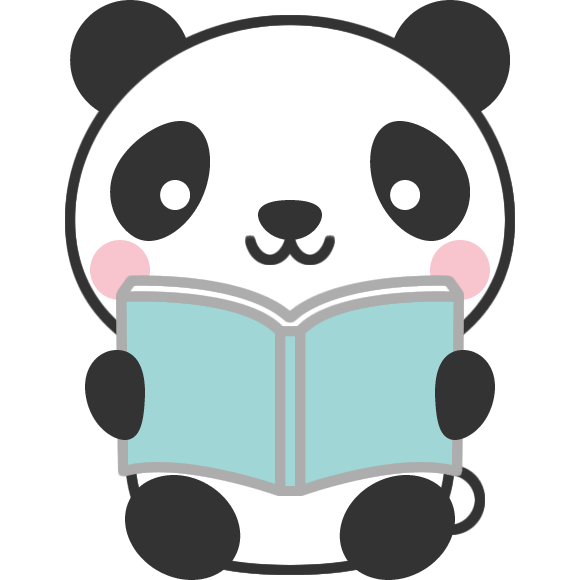
半導体の洗浄工程について解説します!
今回は、「半導体の洗浄工程(種類、目的、タイミング)」について解説していきます。
半導体の洗浄工程について全く知らない方、異分野から半導体の製造工程に関わることになった方など、初心者向けの記事になります。
・半導体の洗浄工程に興味がある
・半導体の製造工程に関わることになった
・半導体の洗浄工程について調べたけど、イマイチ分からない
半導体の洗浄工程【概要】
半導体の洗浄工程とは?(目的)
半導体の洗浄工程とは、シリコンウェハ表面の微小なパーティクル(ごみ)や、金属異物を除去して綺麗にする工程です。
洗浄は、半導体プロセスの中で繰り返し実施され、全体の20〜30%を占める非常に重要な工程です。
通常、半導体を製造するクリーンルーム内は、清潔な状態が維持されていますが、それでも微小なパーティクルを0にすることは出来ません。
一定量以上のパーティクルが半導体製品に付着すると、フォトリソグラフィ工程でパターン不良になったり、ショート不良になることもあります。
半導体製品の微細化・高精度化が進んでいる現在では、洗浄工程の重要性はより高まっています。
洗浄のタイミングは?
続いては、洗浄のタイミングです。
半導体プロセスで洗浄を行うタイミングは、大きく分けて以下の3つです。
①ウェハ入荷時
②成膜前
③削った後
①ウェハ入荷時とは、シリコンインゴットから切り出されたシリコンウェハを、ラインに投入するタイミングです。
シリコンインゴット⇨シリコンウェハへ加工する際や、ハンドリングにより付着した異物を洗浄します。
②成膜前とは、CVDや熱酸化などでシリコンウェハ表面に膜を付ける前のことです。
成膜前に異物が混入していると、膜に異物が混入してしまいます。
一度成膜すると、取り込まれた異物を除去することはできません。
③削った後とは、エッチングや剥離、平坦化後などのシリコンウェハ表面を削った後のことです。
削った後には削りカスが出るため、それが異物として残ってしまう可能性があります。
特に、金属膜などの飾りカスは、半導体素子の電気的特性に悪影響を与える可能性が高いです。
半導体洗浄工程の種類とは?
続いては、半導体洗浄工程の種類です。
大きく分けて、
『「化学的」or「物理的」』
『「ドライ」or「ウェット」』
という風に分類し、それぞれの組み合わせで4つに分けることができます。
「化学的」
⇨薬品を使って化学反応によって汚れを落とすこと。
「物理的」
⇨ブラシなどで直接触れて汚れを落とすこと。
「ドライ」
⇨気体を用いて汚れを落とすこと。
「ウェット」
⇨液体を用いて汚れを落とすこと。
実際の洗浄工程に照らし合わせると、以下のように分類することが出来ます。
①「ウェット」×「化学的」
②「ウェット」×「物理的」
③「ドライ」×「化学的」
④「ドライ」×「物理的」
①「ウェット」×「化学的」は、実際の洗浄工程で最もよく用いられている手法です。
代表的なものに、1960年代に開発されたRCA洗浄と呼ばれるものがあります。
各汚染に対する薬液の組み合わせ、混合比、温度が決められており、複数の薬液によって洗浄を行います。
洗浄の最も代表的な手法ですので、まずはRCA洗浄から学んでいくのが良いでしょう。
洗浄液組み合わせの名称として、APM、HPM、SPM、DHF、BHFなどが使われています。
機会があれば、別の記事で紹介させて頂きます。
②「ウェット」×「物理的」は、超純水を流しながらブラシで擦る手法や、高圧スプレー、超音波を用いる手法などがあります。
シリコンウェハの洗浄以外にも、フォトリソグラフィのマスクを洗浄することもできます。
以上の①、②が「ウェット」による洗浄の手法となります。
現状、実際の工程では99%以上が「ウェット」による洗浄となっています。
③「ドライ」×「化学的」は、プラズマを用いて洗浄対象物を酸化分解する手法です。
洗浄対象としては、酸化分解なので有機物となります。
④「ドライ」×「物理的」は、まだ一般的ではありませんが、極低温エアロゾル洗浄法があります。
アルゴンガスを超低温状態にしてシリコンウェハに吹き付け、洗浄を行う手法です。
以上、半導体の洗浄工程についての説明でした。
参考になった半導体関連本
最後まで読んで頂き、ありがとうございました。
☆この記事が参考になった方は、以下のブログランキングバナーをクリックして頂けると嬉しいです☆⬇︎
コメント